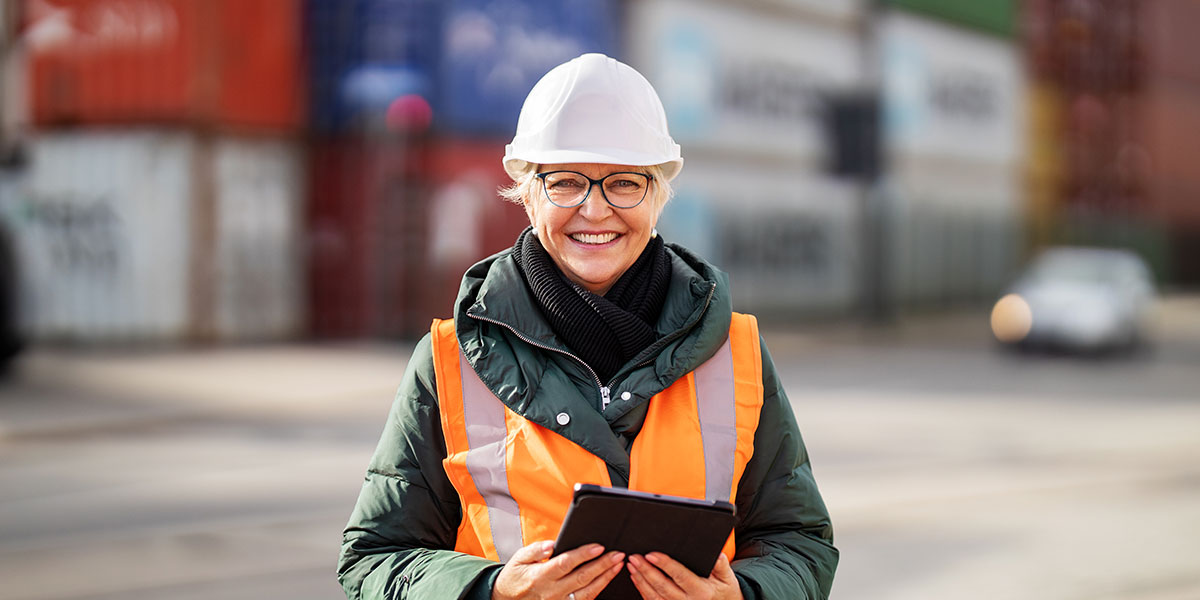
Workplace safety has long been a top priority for companies, and it has become more critical than ever, especially in the transportation, manufacturing, and distribution industries.
The Occupational Safety and Health Administration (OSHA) has created industry standards and regulations to ensure workers' safety during manufacturing, transportation, and distribution operations. These industries face ongoing challenges when it comes to monitoring compliance and managing worker safety in large warehouses and logistics operations.
Fortunately, with advances in technology, automated security systems have become an effective tool for ensuring workplace safety.
In this blog, we'll discuss how automation can help manufacturing, transportation, and distribution companies comply with OSHA standards and keep their employees safe.
What are OSHA Standards?
OSHA standards, also known as OSHA regulations or OSHA requirements, are a set of guidelines and regulations developed by the Occupational Safety and Health Administration (OSHA) to minimize health and safety risks and ensure the safety and health of American workers in various US-based workplaces.
OSHA sets standards for a wide range of industries and types of work, from construction to manufacturing to healthcare and more, with the aim of preventing accidents, injuries, and illnesses that can harm workers and businesses. Employers are incentivized to comply with OSHA regulations with enforcement mechanisms such as inspections, citations, and fines.
Ultimately, adherence to these standards contributes to a more productive and sustainable workplace, protecting an organization's most valuable asset: the health and safety of its workforce.
Why is workplace safety so important?
Workplace safety is a top priority in any industry to ensure the safety of employees and prevent accidents, serious injuries, and loss of life.
Sadly, in 2020, 4,764 workers were fatally injured on the job, with half of those deaths occurring within the manufacturing, distribution, and transportation industries. This means little over 2,000 facility workers did not return home safely to their loved ones.
To ensure the safety of their people, employers have a moral and legal responsibility to implement proper health and safety protocols and follow safety requirements set by OSHA and other industry initiatives such as the CSA program.
It is crucial to establish a safe working environment to cultivate a productive and positive workplace culture. Employers should take proactive steps to ensure the safety of their employees and provide the necessary support to maintain a safe working environment. This can ultimately benefit both employees and the business.
What are OSHA violations?
An OSHA violation occurs when a company or employee knowingly or unknowingly disregards potential or real safety hazards. Compliance safety and health officers, also known as OSHA inspectors, conduct inspections to ensure a workplace operates safely and to identify these violations. These violations do necessarily indicate an incident occurred.
What is the cost of violating OSHA regulations?
Violating OSHA standards is incredibly costly for companies. The manufacturing industry alone received $15,792,567 in penalties from all standards cited, with most violations due to the improper control of hazardous energy, resulting in 369 citations.
OSHA penalties are classified into five categories, including Serious, Other-Than-Serious, and Posting Requirements, costing businesses up to $15,625 per violation. Other categories include Failure to Abate, where companies can be fined up to $15,625 daily beyond the abatement date. Lastly, Willful or Repeated Violations can result in a fine of up to $156,259 per repeated offense.
What are the top 10 OSHA violations in the manufacturing industry?
There are numerous violations in the manufacturing industry. However, some are more common than others. According to OSHA, the top 10 OSHA violations between October 2022 and September 2023 were:
- The control of hazardous energy (lockout/tagout).
- General requirements for all machines.
- Hazard Communication.
- Powered industrial trucks.
- Wiring methods, components, and equipment for general use.
- Mechanical power-transmission apparatus.
- Process safety management of highly hazardous chemicals.
- General.
- Duty to have fall protection and falling object protection.
- General requirements.
Violations of these standards can result in severe consequences, not just for workers but also for employers. It is crucial to be aware of these violations and take necessary measures to prevent them from occurring.
Four ways to improve workplace safety with a security solution
The importance of maintaining a safe workplace cannot be overstated. A robust strategy will help reduce hazards and risk of serious injury and increase compliance with health and safety standards.
Here are four ways businesses can improve workplace safety using a security solution:
1. Communication and protection of hazardous materials
Working with hazardous energy sources and being in their vicinity can result in severe injuries to workers if not appropriately managed. Handling hazardous energy sources is one of the most frequently violated OSHA regulations, highlighting the importance of identifying and classifying these hazards correctly, keeping track of personnel on-site at all times, and implementing appropriate procedures.
Employees who work with machines or equipment classified as hazardous materials may be exposed to these elements, which could lead to physical harm or death if the source is not adequately controlled and maintained.
Proper lockout/tagout practices and procedures can safeguard workers from hazardous energy releases. Organizations can comply with these practices by utilizing access control systems to lock out equipment during specific times.
Businesses can also use a feature such as Tag Boards to track real-time personnel movements during emergencies and improve response time and evacuation management.
Gallagher's Tag Boards feature helps to:
- Actively monitor workers within a zone, on local or remote sites.
- Ensure hazardous energy blast zones have been cleared before explosives are detonated.
- Monitor the movement of people to a muster area during an evacuation.
- Ensure the security control room is aware of workers alone on remote sites.
- Monitor who remains within a high-security area at the end of a working day or shift.
2. Managing people on-site in the event of an emergency
Another reoccurring violation of OSHA regulations includes the improper implementation of maintenance, safeguards, and operational features for exit routes.
In an emergency, companies must ensure that exit routes are not through the path of a high hazard and that all employees are protected during an emergency with alarm systems.
One swipe at a reader at the start of an employee's day enables companies to track and manage employees through multiple access zones and implement other functionality via Gallagher's comprehensive Cardholder Management features.
During an emergency, it is crucial to ensure that all staff members are safe and accounted for. Gallagher's Command Centre software provides a Mobile Evacuation feature that allows for quick identification of employees during an evacuation. This feature displays a list of cardholders within a monitored area, making it easier to ensure all employees have safely moved to a designated safe zone.
Furthermore, Gallagher's Broadcast Notifications Solution enables push notifications in emergencies. These can be automatically triggered by alarms and send critical instructions to multiple recipients in one simple step, such as how to safely exit a hazardous area.
3. Use equipment, heavy machinery, and tools properly
Several OSHA regulations relate to the proper use of equipment, heavy machinery, and tools. An organization's security solution can help ensure employees are following the general requirements for all machinery.
Connecting card readers to machines allows businesses to monitor the time spent by an operator on a machine and limit machine access only to those who are trained and certified to operate them. Gallagher's Competency function provides organizations with the ability to authorize or deny access to a machine based on whether the operator has the proper and current training and certification requirements.
Furthermore, Gallagher's Random Selection function supports you to comply with health and safety requirements such as CSA and OSHA by randomly selecting employees for tests or checks. The feature can be configured to only grant access to the machine or hazardous zone once the operator has completed the necessary testing.
Connecting Gallagher's Alcolizer integration with the Random selection feature further enables businesses to mitigate the risks associated with employees working under the influence of alcohol. The Alcolizer integration provides an easy and practical way to detect breath alcohol levels and prevent access to equipment or areas upon a failed test result.
Automated random personnel selection can be an effective tool for companies to ensure workforce compliance and mitigate risks. This approach ensures a fair and broad group of staff are tested and restricts access to the site or machine until the required tests are completed and passed. By doing so, companies can ensure that safety standards are met and maintained while promoting a culture of fairness and compliance among their employees.
4. Encourage workplace safety
Personal Protective Equipment (PPE) plays a crucial role in maintaining a safe working environment and protecting employees who work with hazardous machinery or substances. Neglecting the use of PPE can lead to injuries and accidents. For instance, eye protection is essential for those who work with sawdust, metal shards, or chemicals. In the United States, thousands of eye accidents occur every day, and 90% of these incidents can be prevented by using appropriate safety eyewear. Companies that make PPE mandatory not only safeguard their workers but also prevent accidents, injuries, and costly downtime.
By integrating lockers with a security system, manufacturing facilities can ensure that employees access their required PPE before they enter the factory floor. Gallagher's Locker Management Solution allows a site to manage locker access, automate allocation, and ensure the best utilization of their locker resources, all from within Command Centre.
Flexible allocation times and a dynamic locker viewer combine to make agile locker use a reality for businesses and automate the usage of PPE within manufacturing, transportation, and distribution facilities.
Gallagher's Locker Management solution is easy to operate. Employees can access their allocated locker by simply presenting their credentials, whether it's a badge or mobile credential, at the Gallagher reader located near the locker bank. The screen will display the locker number and the date/time when access will expire. In the case of multiple lockers, employees can choose which one they want to open.
Gallagher's Locker Management solution offers comprehensive administration visibility. Employees can receive email or SMS notifications regarding their locker allocations before the start of their shift. Site plans can be enhanced by including lockers, which improves situational awareness and site visibility. From the site plan, you can access locker reports, open individual lockers, and view both allocated and unallocated lockers.
Command Centre enables easy viewing of locker activity audit trails, providing insight into usage levels and ensuring employees grab PPE before entering the factory floor.
How will you automate your workplace safety with security?
Workplace safety is not just a regulatory obligation but a fundamental commitment to the wellbeing of employees. The staggering statistics of workplace injuries and fatalities underscore the urgent need for vigilance in adhering to OSHA standards. Employers have a moral and legal responsibility to protect their workforce by implementing proper precautions and safety measures.
The significant financial ramifications of OSHA violations should be a stark reminder of the potential costs involved. Companies must understand that neglecting safety protocols endangers lives and creates costly downtime, jeopardizing the bottom line.
The four ways to improve workplace safety through automated security systems covered in this blog emphasize the importance of communication, proper management, equipment usage, and encouraging the use of Personal Protective Equipment (PPE). These practical strategies automate health and safety, safeguard employee's wellbeing, and contribute to greater operational efficiency and security within a facility.
Ultimately, it is vital to understand security's critical role in workplace safety, not just as a legal necessity but as a core component of responsible and ethical business operations. By prioritizing workplace safety and adopting the recommended security measures, companies can protect their most valuable assets their employees, and create a safer, more efficient work environment for all.